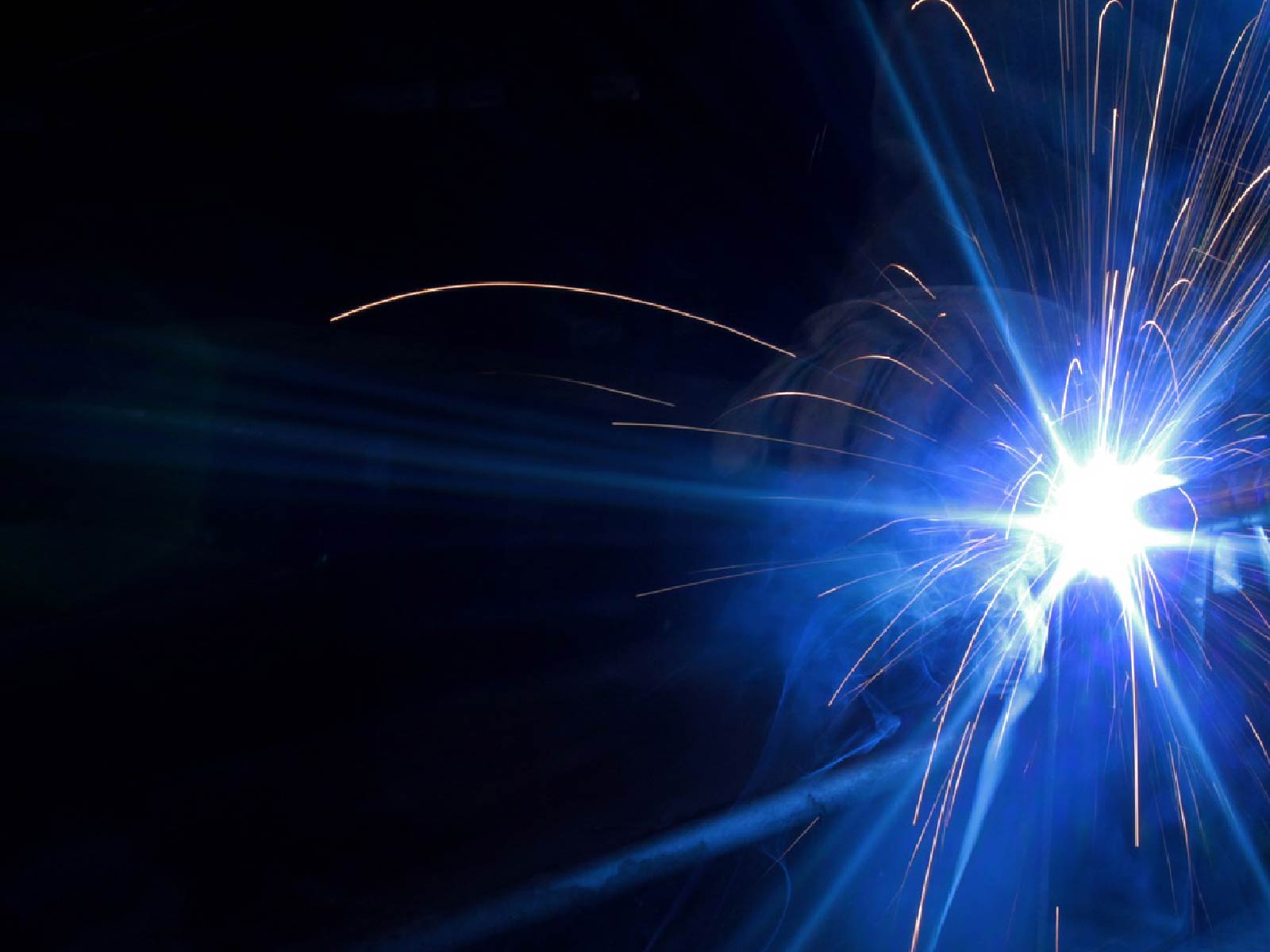
Weld Quality Inspection: The Role of Machine Vision in 2025
What does it take to create a world-class manufacturing experience?
Is it the safety of welded joints? Compliance? Structural integrity? The answer is simple. A bit of everything!
As days go by, advanced tech integration is becoming imperative to quality manufacturing. And that’s where weld quality inspection comes in. With machine vision in the picture, the industry is set to reimagine precision and efficiency like never before.
This article discusses the pivotal role of weld quality inspection, the benefits of machine vision in welding, the role of weld monitoring cameras, industry applications, and future trends. Keep scrolling!
Why Weld Quality Inspection Is Important?
From construction to aerospace, welded joints are integral to every industry to keep it safe and avoid financial losses and machine failures. Now, traditional inspection methods aren’t much help here as visual assessments and manual measurements are time-consuming. Being a human-driven process, they are also prone to errors. So, automated weld quality inspections are the need of the hour.
However, optimum weld quality isn’t just limited to post-weld inspection. Real-time weld monitoring is also a crucial aspect of weld integrity. Seamless tracking and analyzing of vital parameters like heat input, alignment, and speed can mitigate potential issues with time. In turn, it significantly lowers the chance of rework and product defects.
Besides, there are times when the project demands are odd. Say the welds in a structural steel project that might fail to meet the acceptance criteria for designated codes. In worst cases, it could pose a threat to serious injury and even loss of life.
Pipes and tanks carrying hazardous chemicals can also have a dangerous impact on the environment. Imagine humans coming in close contact. That’s a risk no one wants to take. That’s why automated weld quality inspection and real-time monitoring are mandatory.
The Paramount Role of Machine Vision in Welding
Powered by cameras and image processing algorithms, machine vision is pushing the boundaries of weld quality inspections. From accurate measuring of weld dimensions to detecting surface defects, it ensures compliance with real-time feedback for corrective actions. For manufacturers eyeing top-class weld quality, machine vision ticks all necessary boxes.
- Unmatched accuracy: Machine vision systems effortlessly detect minute defects that are often overlooked by human inspectors.
- Increased Efficiency: Automated weld quality inspections lessen the time needed for quality checks, thereby speeding production cycles.
- Improved Data Collection: It helps gather valuable information for further analysis and improving welding techniques and allied processes.
Take robotic welding applications for instance. A one-of-a-kind setting where machine vision is a preferred choice to train robots in enhancing welding. This is generally done by training the robots to adapt to varied geometry and part positioning.
Weld Monitoring Cameras: A Befitting Application of Machine Vision
Weld monitoring cameras have unlocked unique applications for machine vision. They are specially designed to operate across multiple challenging environments during a typical welding process. No matter how intense the light and heat, weld monitoring cameras are capable of capturing high-quality images.
Here’s a closer look at the top features of weld monitoring cameras that make them a rewarding choice for machine vision applications.
- HDR Imaging: High definition range helps with clear visualization of bright arcs and darker surrounding areas for a comprehensive weld quality inspection.
- Real-Time Monitoring: Helps in prompt detection of defects and suggesting corrective measures.
- Versatility: Uniquely compatible with a range of welding techniques like TIG, MIG, plasma welding, and more.
- Thermal Imaging: Cameras equipped with thermal imaging plays a rather vital role in monitoring heat distribution as well temperature profiles to boost weld quality.
For example, Xiris weld monitoring cameras are a class apart in HDR imaging. They are readily suitable for monitoring the steps of open arc welding. No wonder they are an industry-preferred choice for leading manufacturing divisions.
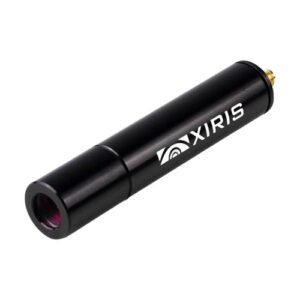
XVC-310 – Lipstick Weld Camera from Xiris
Key Industry Applications of Monitoring Cameras for Weld Quality Inspection
Weld monitoring cameras find its use across multiple industries, each with significant benefits in terms of quality production and efficiency. As advanced systems, the monitoring cameras offer real-time insights into all welding operations. Thus, they dramatically reduce defects, boost overall efficiency, and promise unmatched precision. Here’s how key industries are benefiting from this rewarding tech.
Automotive Manufacturing
Weld monitoring cameras are a game changer for automotive manufacturing, especially in boosting precision control for high-volume production. They have not only mitigated the likelihood of defects for critical components but also helped identify potential defects and reduce rework. Together, they have upped the standards for product reliability, a sharp contrast to manual weld quality inspection bogged down by frequent downtime sessions.
Aerospace
Similar to automotive manufacturing, the aerospace industry demands meeting stringent safety and quality protocols. With weld monitoring cameras, aircraft structure manufacturing has been able to meet critical parameters. From specifications to certifications, maintenance to safety contribution, machine vision cameras are winning it big in weld quality inspection.
Energy Sector
The reliability of renewable energy installation and pipelines for welding has plagued the energy sector for decades. However, with machine vision monitoring, things are changing for the better. Take pipelines, for instance, where weld seam durability helps mitigate leaks and failures. Also, predominantly for renewable energy installations, monitoring cameras are a primary requirement for a robust infrastructure.
General Manufacturing
General manufacturing comprises a range of welding applications. By deploying weld monitoring cameras, companies can effectively streamline welding operations for various materials. This is a step toward eliminating manual weld quality inspection, minimizing scrap rates, improving product quality, and boosting overall profitability.
Machine Vision in Research and Education
Besides commercial and industrial applications, machine vision is also opening newer frontiers in the world of education and research. Thanks to the inherent capability of machine vision that helps capture real-time visuals of complex processes in a precise manner. This has further led to new opportunities for improved training, advanced knowledge, and fostering innovation across the field of welding.
For what matters, machine vision is widening the scope of research and education across two significant fronts.
- Advanced studies: Modern-day researchers prefer using machine vision to analyze welding processes, thereby facilitating innovation across different materials and techniques
- Educational Practice: Educators are using real-time visuals and recordings to help students gain a comprehensive understanding of welding concepts. Specialized learning options like weld camera educator packages, for instance, add to a safe and immersive learning experience and improve training outcomes.
Machine Vision and Weld Monitoring- A Rewarding Future Awaits
Industry reports indicate a rather steady growth for the machine vision industry, with a CAGR of 8% by 2027. Similar to most tech fields today, artificial intelligence is the highest growth contributor-the prime force behind defect detection, boosting efficiency, and preventive maintenance.
Further, there’s Big Data for great operational insights and driving continuous enhancement. Centralized data management, along with remote monitoring is also helping to streamline operations and enabling real-time decision-making.
Say Yes To The Winning League For Weld Quality Inspection With Machine Vision
Efficient, precise, and real-time monitoring has enabled machine vision to revolutionize weld quality inspection for multiple industries. Driving the transformation are specialized tools like weld monitoring cameras that ensure welded components bespeak the highest standards of quality.
At HWYL, we are an authorised partner for Xiris Weld Cameras, helping next-gen businesses with top-of-the-line weld monitoring solutions. This rewarding tech can be a game changer helping you achieve superior weld quality, boost productivity, and ensure safety and reliability of your products.