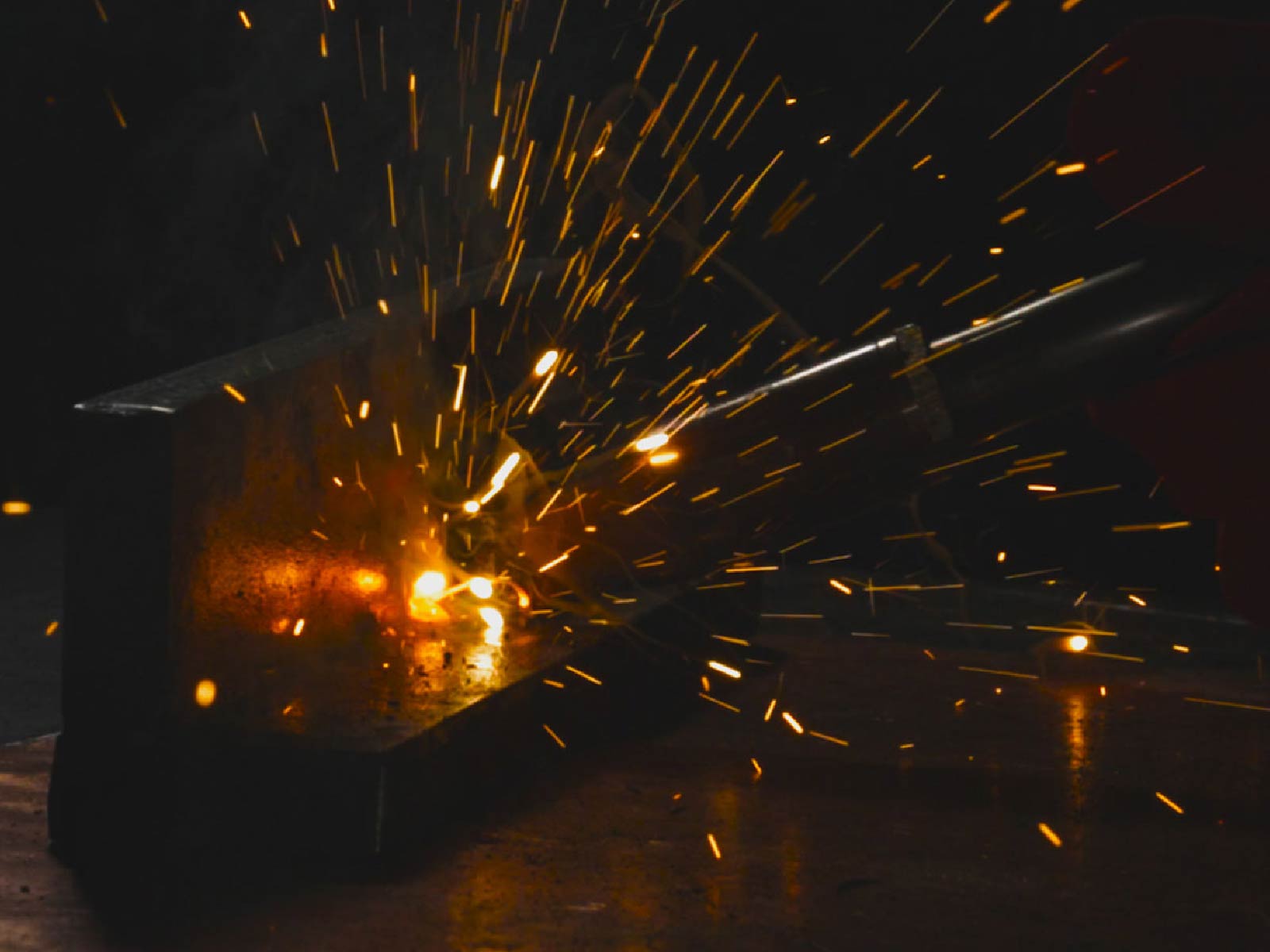
Weld Monitoring in Heavy Industries: Advancing Quality with Machine Vision
In sectors like shipbuilding, aerospace, and infrastructure, welding forms the backbone of structural integrity. The quality of these welds directly impacts safety, durability, and regulatory compliance. Traditionally, industries have relied on post-weld inspection to detect flaws, but this approach can be reactive, costly, and sometimes too late. That’s where real-time weld monitoring comes in, enabling smarter, faster, and more accurate welding operations with the power of advanced machine vision.
In this article, we explore how weld monitoring is transforming heavy industries, what welding methods are involved, and the role of technologies like HDR and SWIR imaging.
Welding in Heavy Industries: A Sector-Wise Overview
1. Shipbuilding
Welding is used extensively in constructing hulls, decks, and bulkheads. Techniques like Gas Metal Arc Welding (GMAW), Flux-Cored Arc Welding (FCAW), and Submerged Arc Welding (SAW) are common, especially for joining large steel components. Given the scale and complexity, weld consistency is crucial, making real-time monitoring essential for detecting irregularities early.
2. Aerospace
Aircraft structures demand extremely precise welds, often involving Tungsten Inert Gas (TIG) and laser welding. Lightweight materials like titanium and aluminum alloys are sensitive to heat and prone to distortion. Weld monitoring here ensures micron-level accuracy, especially for critical joints in engine assemblies and fuselage sections.
3. Railway
Rail manufacturing and carriage assembly use MIG welding (Metal Inert Gas welding), flash butt welding, and spot welding. Since these welds endure repetitive stress over time, quality control is vital. Monitoring systems help maintain alignment and prevent defects during automation-heavy production processes.
4. Oil & Gas / Pipeline Fabrication
Pipeline welding often involves orbital welding or automated GMAW, especially for high-pressure environments. Defects like porosity or misalignment can have catastrophic consequences. Real-time monitoring helps ensure joint integrity, even under harsh outdoor or offshore conditions.
5. Construction & Infrastructure
Steel frameworks, bridges, and rebar cages depend on reliable arc welding. Given the scale and timeline of construction projects, continuous monitoring accelerates productivity without compromising safety.
6. Power Generation (Thermal & Nuclear)
Welding in power plants involves manual TIG (Tungsten Inert Gas welding), GTAW (Gas Tungsten Arc Welding), and automated welding for components like boilers, reactors, and turbine housings. These require absolute precision. Monitoring ensures compliance with stringent codes and reduces rework in high-cost environments.
Weld Monitoring vs. Weld Inspection: What’s the Difference?
Traditional weld inspection methods, like ultrasonic testing, radiography, or dye penetrant tests, are performed after welding is complete. While effective, they are often time-consuming and may fail to catch transient or process-related defects in real time.
Weld monitoring, on the other hand, provides live visual and analytical data during the welding process. With machine vision cameras mounted near the weld zone, operators can observe arc behavior, seam alignment, and molten pool characteristics as welding progresses.
Key Advantages of Weld Monitoring
Early detection of defects and process deviations
Real-time feedback allows operators to identify issues like misalignment, porosity, or inconsistent weld pool behaviour as they happen, reducing the chance of faulty welds progressing unnoticed. In the aerospace sector, this level of precision is vital for ensuring safety in flight-critical components.
Reduced scrap, rework, and production delays
By catching defects early, weld monitoring minimizes wasted materials and rework time. For railway and shipbuilding, this means greater throughput and lower operational costs on large-scale projects.
Seamless integration with automated welding systems
Modern weld monitoring systems integrate with robotic arms and automated production lines, enabling adaptive control. This is especially beneficial in pipeline fabrication, where consistent weld quality is essential across long seams.
Improved training and documentation through video records
Recorded weld data and visuals support training, audits, and quality reviews. In power generation, where traceability and compliance are critical, this ensures long-term operational integrity and accountability.
Machine Vision Technologies Powering Weld Monitoring
High Dynamic Range (HDR) Imaging
Welding generates intense light from the arc, along with dark areas around the workpiece. Standard cameras fail to capture such contrast. HDR imaging enables clear visibility across the full brightness spectrum, allowing precise visualization of the weld pool, arc, and surrounding surfaces, even under glare and smoke.
Short-Wave Infrared (SWIR) Imaging
Welding environments often involve smoke, spatter, and high heat. SWIR cameras cut through these visual obstructions by capturing wavelengths beyond visible light, providing a reliable view of the weld pool and seam. This is especially useful in high-speed automated welding and for reflective or coated metals.
Why Heavy Industries Need Weld Monitoring Today
From reducing rework and production downtime to improving safety and compliance, the benefits of weld monitoring are extensive. For industries operating at scale or under stringent quality standards, real-time monitoring helps maintain consistency and avoid costly failures.
Modern weld monitoring systems are built to perform in demanding industrial environments and are compatible with various welding methods and materials. They support continuous improvement by providing live data, video records, and integration with automated processes, helping manufacturers stay competitive in a rapidly evolving landscape.
Building a Safer, Smarter Future with Weld Monitoring
Heavy industries demand precision, consistency, and efficiency, and real-time weld monitoring delivers exactly that. With advanced imaging technologies like HDR and SWIR, manufacturers can detect defects early, reduce downtime, and improve overall quality control.
At Hwyl, we provide access to cutting-edge weld monitoring solutions from global leaders like Xiris. Whether you’re in shipbuilding, aerospace, or power generation, our systems are engineered to perform in demanding industrial environments.
Connect with us today to explore how intelligent weld monitoring can modernize your welding operations and strengthen your competitive edge.